Simple Change works best
By Steven Crowden
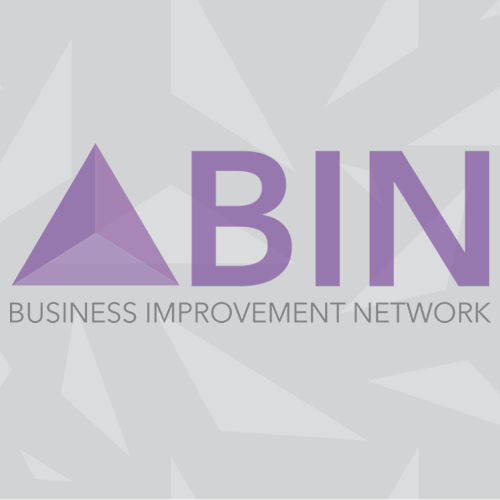
What is Simple Change?
From my experience, over a number of years, I have seen that change can be put forward as this large, encompassing behemoth of a solution to all a firm’s issues.
It has in some places I have worked, been applied company wide, with all departments and teams expected to incorporate this into their daily work schedule. This is while being expected to complete the tasks already assigned to them. I have rarely seen it last.
This sounds very negative, but although true, I am saying this as a comparison to how I believe change should be approached and where I have seen it work best.
Simple Change is a light touch approach to making changes. Only gathering data where and when required, with the expectation of highlighting issues within known areas of concern. Then utilising specific tools and approaches to solve the highlighted issue.
To explain this further I have detailed 3 examples of where I have used this approach.
Example 1 – Process Consolidation
Situation
Working for a high street bank. They had multiple locations where the same process was completed. However, through simple measurement they identified the issue that the volume of output between the 3 teams varied greatly. The aim was to increase output by establishing the best practise for the process.
Method
Through observation and conversation, I highlighted where the approach and process used differed. I confirmed that the purpose of the process, the systems used, also the inputs and outputs were all consistent.
An experienced member of each team travelled to a central location with the aim of process mapping the one best way of working. We worked through the stages of the process. Each person gave their version of the stage, we discussed the pros and cons and determined the best approach to map. Process elements were taken from all the people attending.
What was interesting was the way, over time, that individuals had developed process shortcuts, or system shortcuts. People completing the process on a daily basis can be a great source of improvement, before moving to IT solutions.
Outcome
Completed in 1 day. The participants reviewed the map with colleagues to confirm nothing had been overlooked. The new process was rolled out and each area increased their output, some more than others.
Example 2 – New Customer Form
Situation
This company gained new customers weekly. Customer details and requirements were gathered via a paper form and entered onto the system. The form was 6 pages long, and the alignment of the form to the computer screens was lacking.
Method
It was decided that the driver of the best process would be what was required by the system, so I sat with the person who keyed in the information.
We reviewed each piece of information the system required, aligning this with the form layout. The questions were numbered in the correct order. Some were removed if not required, large areas where reduced where the amount of information needed did not align with the space given. And even questions added that were not on the original form but required by the system.
Outcome
I produced a prototype of the new form, which was 3 pages long; in the order the data was entered onto the system and with the correct space required for answers. The form was reviewed by the salespeople completing the information to ensure nothing was missed. The new form was more user friendly, quicker for the customer to complete and quicker to enter onto the system.
Example 3 – Manual Collation
Situation
During the main COVID period, I was working at a site in the midlands that used manual labour to collate the elements of the laboratory COVID testing kit. The operation was 24/7 and produced 10’s of 1000’s of kits each day. The aim was to increase production to hit government targets.
Method
As the operation was 100% manual (which would not change), the method was to watch the approach utilised by the hundreds of workers. There was a large range of experience and enthusiasm, but with the aim being to increase the volume of output, while maintaining quality, the answer was with the people completing the process.
The process of collation was broken down into sections. These were the initial movement of items for the kit and layout of the working area, the collation of the numerous items and finally the quality check and movement of stock away from the work area.
Outcome
The best elements of speed and accuracy were taken and formed the new process. This was reviewed by several of the current workforce. A model process line was produced. Over a period of 3 days, I rolled out the training to every single person across all the shifts. We used the team leaders to monitor the new process was being adhered to. The output increased by the required amount to begin to hit the targets.
In Conclusion
Simple Change can be used in areas where specific problems have occurred. This does not mean the approach is to simply turn up and change processes. There are still guidelines to follow when gathering data and when rolling out change which are important in all change methods. Hopefully you can see that small, quick, effective change does not have to be accompanied by company wide initiatives. Small teams and departments can achieve positive change with a simple approach to change which is within their control.
About the author
Steven Crowden has been a Process Improvement Consultant for over 15 years and worked in multiple industries from Banking to Telecommunication, and Publishing to Mining. In 2023 he published his book “Simple Change – A Practical Guide”.
Enjoyed reading these articles?
Have you got something you can share with the Network. Why not submit an article